Revolutionizing the Automotive Industry: The Role of Injection Molding
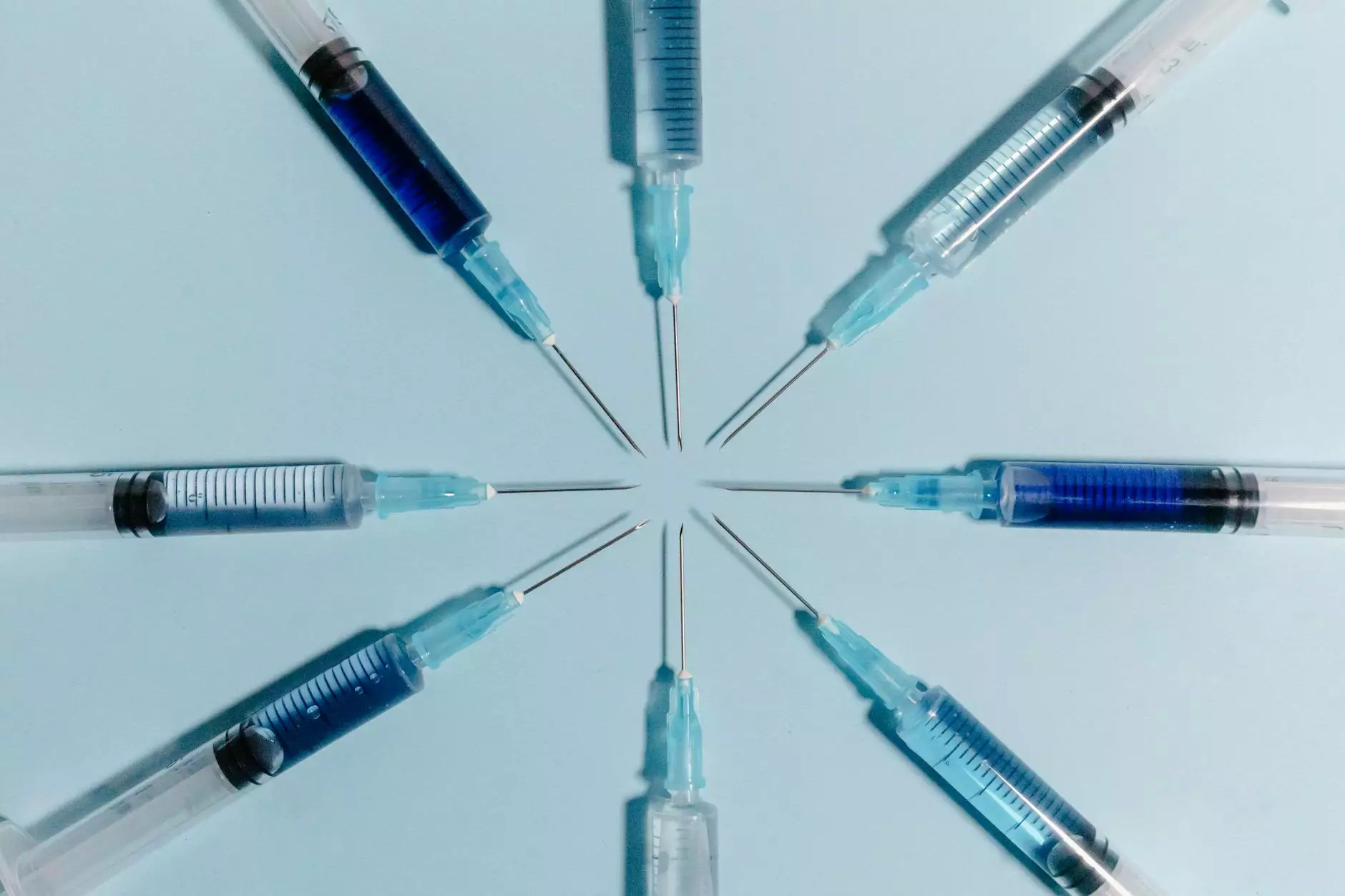
The automotive industry stands at the forefront of innovation and technology, with manufacturers constantly seeking methods to enhance vehicle performance and reduce production costs. One of the pivotal techniques leading this change is injection molding automotive, a process enabling the creation of complex and high-precision parts for vehicles. This article delves deep into the world of injection molding, its advantages, applications in the automotive sector, and how it shapes the future of vehicle manufacturing.
Understanding Injection Molding in Automotive Manufacturing
Injection molding is a manufacturing process that involves injecting molten material into a mold to create parts. This technique is especially beneficial in the automotive sector due to its ability to produce high volumes of intricate components with a variety of materials, including thermoplastics and thermosetting polymers.
How Injection Molding Works
The injection molding process can be broken down into a few essential steps:
- Mold Design: Engineers create a detailed design for the mold based on the specific part required.
- Material Selection: Appropriate materials are selected, often depending on their properties such as strength, weight, and resistance to certain elements.
- Melting the Material: The chosen material is heated until it becomes molten.
- Injection: The molten material is injected into the prepared mold at high pressure.
- Cooling: The material cools and solidifies within the mold, taking its shape.
- Demolding: The solidified part is removed from the mold.
Common Materials Used in Automotive Injection Molding
Injection molding in the automotive industry utilizes a variety of materials suited to different applications, including:
- Thermoplastics: Such as polypropylene (PP), acrylonitrile butadiene styrene (ABS), and polycarbonate (PC).
- Thermosetting Plastics: Resins that solidify during the molding process and cannot be remelted.
- Elastomers: Providing rubber-like flexibility, commonly used for seals and gaskets.
Advantages of Injection Molding in Automotive Applications
The incorporation of injection molding offers numerous advantages for automotive manufacturers, making it a preferred choice in many scenarios. Below are some of the key benefits:
1. Cost-Effectiveness
One of the primary advantages of injection molding is its cost efficiency. Once a mold is created, it can produce thousands of parts with minimal variation. This reduces the cost per part significantly when producing large quantities.
2. Design Flexibility
Injection molding allows for a vast range of design possibilities. Manufacturers can create complex geometries and thin-walled components that can be difficult or impossible to achieve with traditional manufacturing methods.
3. Consistency and Repeatability
The injection molding process is highly automated, ensuring that each part produced is identical to the last. This consistency is crucial in the automotive industry where precision is paramount.
4. Material Variety
Injection molding supports a wide range of materials, enabling manufacturers to select the best material for each part’s functionality. This flexibility leads to improved performance features such as lightweight components that help enhance fuel efficiency.
5. Reduced Waste
Compared to traditional manufacturing processes, injection molding generates less waste. Once the mold is created, excess material can often be reused, leading to further cost savings and environmental benefits.
Applications of Injection Molding in the Automotive Sector
In the automotive industry, injection molding is employed in numerous applications, particularly for parts that require durability, strength, and aesthetic appeal. Here are some common applications:
1. Interior Components
Injection molded parts often include interior components such as:
- Dashboard Panels: Offering both functionality and aesthetic appeal.
- Door Panels: Lightweight and designed for integration with various controls.
- Console Components: Providing storage solutions while enhancing visual appeal.
2. Exterior Components
Automotive exteriors increasingly leverage injection molding for parts like:
- Bumpers: Designed for impact resistance and airflow management.
- Grilles: Offering both protection and style to the vehicle’s front.
- Fenders: Lightweight options that contribute to overall vehicle efficiency.
3. Functional Parts
Injection molding also produces critical functional components such as:
- Fuel Tanks: Engineered for safety and efficiency.
- Electrical Housings: Providing protection for sensitive components.
- Connectors and Fittings: Essential for various systems within the vehicle.
The Future of Injection Molding in Automotive Manufacturing
As technology advances, the role of injection molding in automotive manufacturing is poised to grow even further. Innovations such as 3D printing and smart molds are set to enhance the efficiency and capabilities of the injection molding process.
1. Advancements in Materials
The development of new materials, such as biodegradable plastics and enhanced composites, will allow manufacturers to create even more sustainable and efficient automotive products without compromising on performance.
2. Integration with Automation and AI
Automation and artificial intelligence are already finding their way into the injection molding processes in automotive manufacturing. This integration promises to streamline production, reduce labor costs, and increase overall efficiency.
3. Sustainability Initiatives
With environmental concerns becoming increasingly paramount, the automotive industry is focusing on sustainability. Injection molding processes can be adapted to utilize recycled materials, further contributing to a circular economy.
DeepMould: A Leader in Injection Molding Solutions
At DeepMould.net, we specialize in providing high-quality injection molding automotive solutions. Our expertise in metal fabrication allows us to deliver superior parts for varied automotive applications. Our commitment to innovation ensures that we stay ahead of industry trends, offering our clients the best solutions for their manufacturing needs.
Why Choose DeepMould?
Choosing DeepMould means partnering with a firm dedicated to quality and excellence:
- Expertise: Our experienced team possesses deep knowledge of injection molding processes and materials.
- Quality Assurance: Rigorous testing and quality checks ensure each product meets industry standards.
- Customer-Centric Approach: We work closely with our clients to understand their needs and deliver tailored solutions.
Conclusion
Injection molding is a transformative process within the automotive industry. With its cost-effectiveness, design versatility, and consistent quality output, it significantly influences vehicle manufacturing. At companies like DeepMould, the utilization of advanced injection molding techniques continues to shape the future, driving innovation and efficiency. As the automotive industry evolves, so does the capability and application of injection molding, promising a brighter, more sustainable future for manufacturers and consumers alike.