The Transformative Impact of Electric Injection in Metal Fabrication
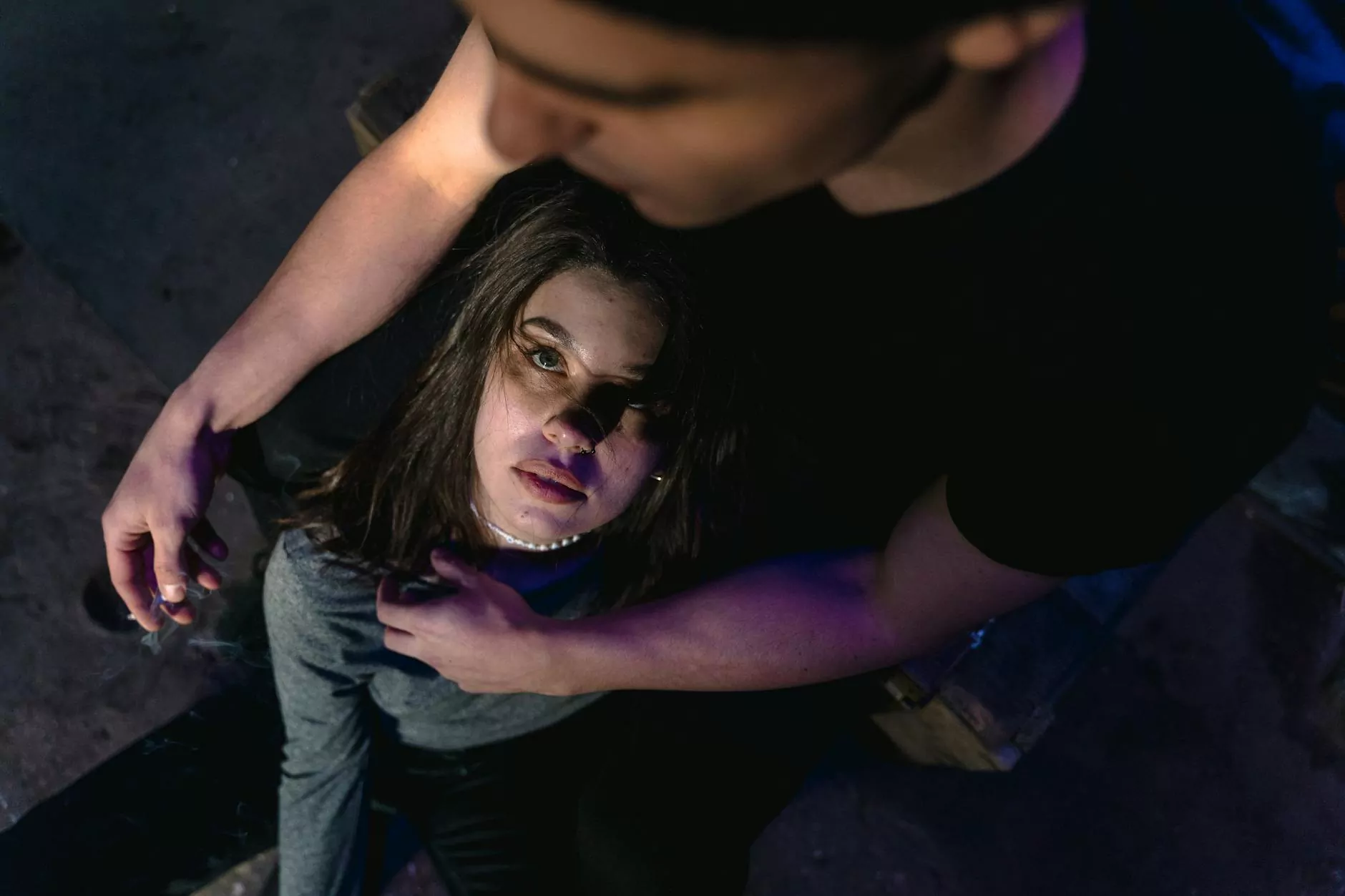
Understanding Electric Injection Technology
Electric injection technology represents a significant advancement in the realm of precision manufacturing and metal fabrication. This innovative process utilizes electrical energy to facilitate the injection of molten metals into molds, which enhances production efficiency and quality control. By eliminating hydraulic systems traditionally used in injection molding, the electric injection method offers higher control over the process, leading to more uniform results and reduced waste.
Key Advantages of Electric Injection in Metal Fabrication
The integration of electric injection technology into metal fabrication processes comes with numerous advantages:
- Enhanced Precision: With advanced control algorithms, electric injection allows for better temperature and pressure regulation, resulting in high precision in the final products.
- Improved Energy Efficiency: Electric systems consume less power than their hydraulic counterparts, translating to lower operational costs.
- Reduced Cycle Times: The rapid heating and cooling capabilities of electric systems expedite the production cycle, leading to faster turnaround times.
- Lower Maintenance Costs: Electric injection systems generally have fewer moving parts compared to hydraulic systems, which reduces wear and tear and requires less maintenance.
- Environmentally Friendly: By using electric power, this technology minimizes the reliance on hydraulic fluids, thus contributing to a lower ecological footprint.
Applications of Electric Injection in Metal Fabrication
Electric injection technology has found applications across a range of industries due to its versatility and effectiveness. Some of the sectors that benefit from this innovative approach include:
- Aerospace: Precision parts are manufactured with extreme accuracy, which is critical in aerospace applications.
- Automotive: Electric injection is used in the production of complex components that demand high quality and repeatability.
- Consumer Electronics: The production of lightweight and durable enclosures and components is enhanced through electric injection.
- Medical Devices: In the medical field, the need for precision and hygiene is paramount, making electric injection a preferred choice.
Why Choose Deep Mould for Electric Injection Solutions?
At Deep Mould Inc., we pride ourselves on being at the forefront of the metal fabrication industry. Here's why our electric injection solutions stand out:
Expertise and Innovation
Our team consists of seasoned professionals who specialize in leveraging electric injection technology to produce high-quality components. We invest in the latest machinery and technology to ensure our clients benefit from cutting-edge solutions.
Customized Solutions
We understand that no two projects are identical. Thus, we tailor our services to meet your specific requirements, optimizing processes and materials for the best outcomes imaginable.
Commitment to Quality
Quality assurance is at the heart of our operations. We conduct rigorous testing and quality checks to ensure that every part produced meets the highest industry standards.
Sustainability
Deep Mould is committed to sustainable manufacturing practices. The use of electric injection not only reduces our carbon footprint but also helps our clients meet their own sustainability goals.
The Future of Electric Injection in Metal Fabrication
The future of electric injection in metal fabrication looks incredibly promising. As technology evolves, we can expect the following trends to shape the industry:
- Increased Automation: The integration of AI and machine learning into electric injection systems will enhance automation, resulting in smarter manufacturing processes.
- Advanced Materials: Research into new materials that can be effectively molded using electric injection will broaden the scope of applications.
- Greater Customization: Demand for custom parts will drive innovations in electric injection technologies that allow for quicker adjustments in production lines.
- Global Expansion: As more businesses recognize the benefits, electric injection technology will proliferate globally, creating new partnerships and markets.
Conclusion: Embracing the Electric Injection Revolution
In conclusion, the adoption of electric injection technology is revolutionizing the way metal fabrication is conducted. Its benefits, from enhanced precision to environmental sustainability, cannot be overlooked. By partnering with industry leaders like Deep Mould Inc., businesses can ensure they are leveraging the best-in-class technology to stay ahead in a competitive market.
For more information about our electric injection solutions and how we can help your business thrive, visit our website at deepmould.net.